Huazhuo Plastic Welding Expert
When to use hot-plate welding
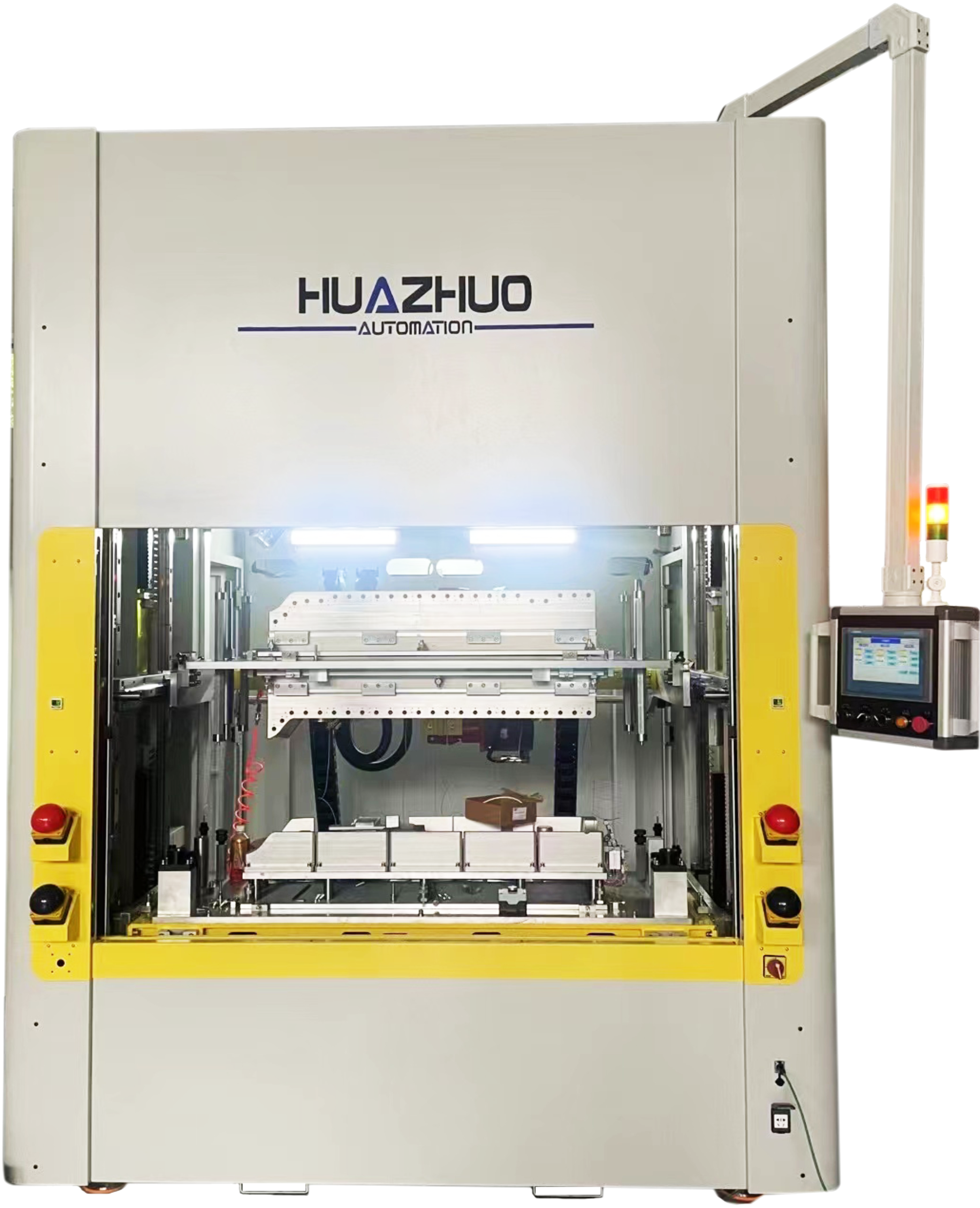
When considering the common plastics joining methods for assembling a new product, hot-plate welding should be in the mix. This low-force method of heating and bonding plastic parts has been around for a long time. Contemporary machinery and tooling provide users with exceptional control and consistent weld results.
When is Hot-Plate Welding the Better Choice?
The hot-plate welding process is typically considered under certain conditions. Here are some factors where it outperforms other methods:
The parts are larger: this factor may rule out ultrasonic welding.
The product geometry is complex: complexity could hinder the use of vibration welding.
Excessive or loose particulate (flash) is unacceptable.
A-surface part marking is not permissible.
High strength and hermetic seal are required for the assembly.
An assembly/machine cycle time in the 15-25 seconds range is acceptable.
Why Choose Hot-Plate Welding?
Beyond these conventional reasons, there are additional facts to mull over:
Small assemblies: Hot-plate welding is not just for large components. Leading manufacturers offer models designed for parts no larger than 6” square.
Simple geometry components: These also benefit from the low-stress, high-strength results of hot-plate welding.
Flash control: Even if not a high priority, who wouldn’t appreciate controlled flash?
Part marking: This is often an unintended side effect of energy misdirection. It may cause rejected assemblies due to inconsistencies in weld results.
Robust processing window: The performance of the hot-plate welding process is generally very robust, which is beneficial for operational efficiency.
Speed of welding: If hot-plate welding cycle times are not fast enough, consider welding multiple parts simultaneously.
The Advantages and Disadvantages of Hot-Plate Welding
Like all methods used to join plastic components, hot-plate welding has its pros and cons. Certain resin and filler combinations can be challenging or impractical to weld with this method. If the equipment does not offer velocity, distance, and force control, process control capabilities may be limited. Additionally, without suitable coating surfaces on the heated tooling, tool wear and plastic material sticking can become issues.
Despite these potential Disadvantages, a well-equipped hot-plate welder with well-engineered tooling can provide an excellent solution for assembling plastics.