Huazhuo Plastic Welding Expert
coating equipment promotes the development of automotive interior
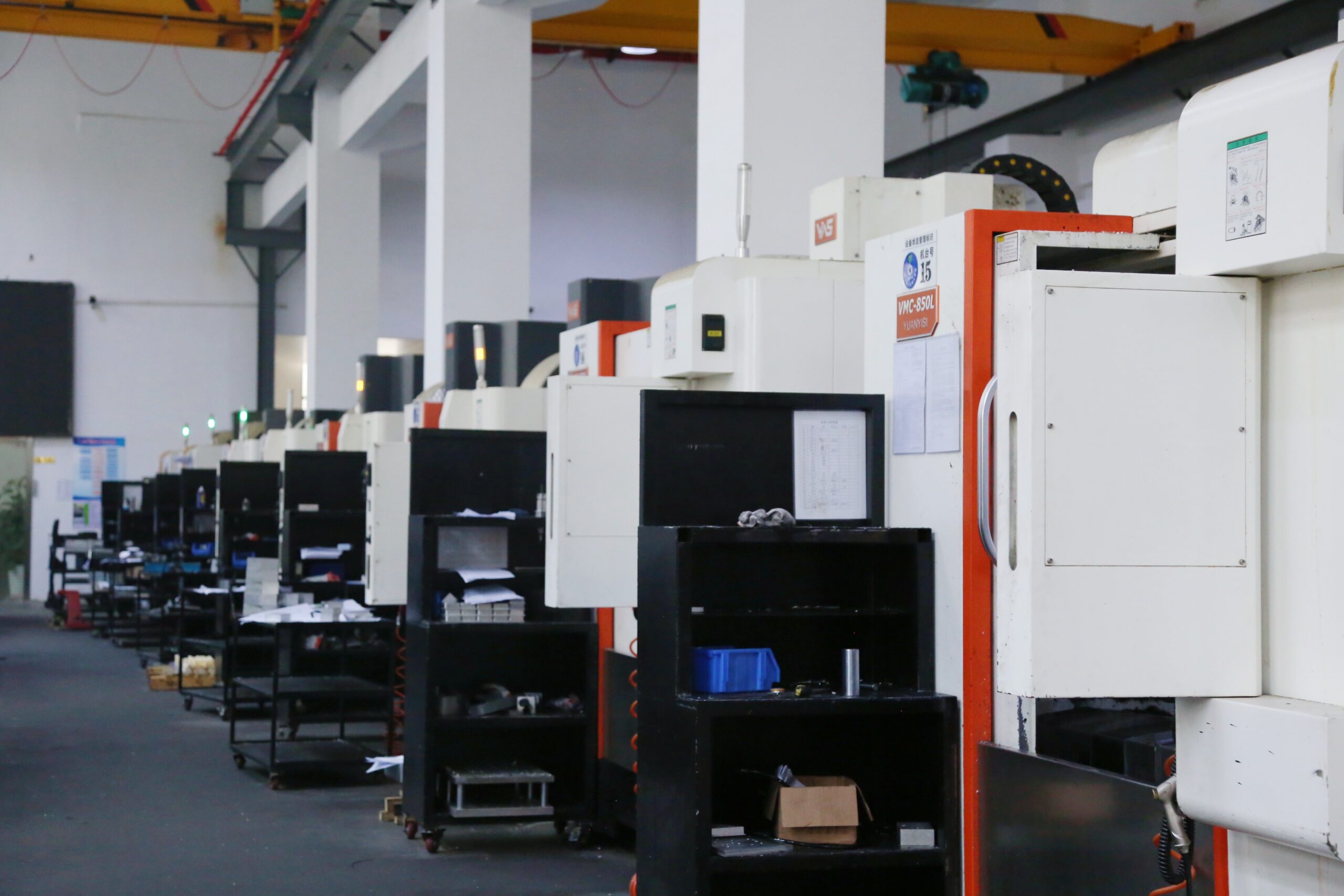
With the fast development of the automotive industry, people’s constant improvement of perfect requirements of the automotive interior, including the surface of the instrument panel, auto door, and center console, are all required to be covered with soft leather. Huazhuo focuses on the most advanced pressing coating technology.
The coating equipment is an automated device specially used to wrap and fix flexible materials (such as leather, cloth, etc.) on substrates (such as automotive interior parts, furniture parts, etc.).
The process flow is as follows
punching (cutting) → sewing → glue spraying → line pre-wrapping → pressing and corner wrapping.
The principle of coating equipment
Heating system: Heating is one of the core parts of the coating equipment. It is responsible for heating the coating material (such as leather, cloth, etc.) to a certain temperature to activate the glue or adhesive on its surface.
Principle: Heating systems usually use electric heating elements, such as heating tubes and plates, as the heat source to generate heat through current heating. The heat is then transmitted to the coating material by conduction, convection, or radiation, gradually increasing its surface temperature to the required range. Meanwhile, the heating system is installed with a temperature control system for real-time monitoring and adjustments of the heating temperature to guarantee that the coating material reaches the best temperature for coating.
Pressure system: This is usually responsible for applying the right amount of pressure so that the heated coating material sticks as closely as possible to the substrate during the coating process. This step is quite important in removing bubbles and enhancing the flatness and quality of the coating.
Principle: Most of the pressure systems include actuators like cylinders, hydraulic cylinders, or servo motors, which are capable of creating appropriate pressure based on the pre-set program or instruction from operators. The actuator, in this case, is responsible for driving parts like the pressure head or pressure roller, which press against the coating material and substrate during coating to make them come in close contact and stick to each other. Meanwhile, the pressure system is simultaneously designed with a pressure sensor and control system that can monitor and regulate the pressure automatically in real-time to secure stability and consistency in this coating process.
Control system: The control system is the “brain” of coating equipment. It coordinates the work of various systems and ensures that the coating process is accurate and efficient.
Principle: The control system, adopting PLC, precisely regulates the heating system, pressure system, pressure system, and other auxiliary systems with precision. The control system is allowed to get information from such input devices as sensors and operation panels, accomplish data processing, and make logical judgments according to the presenting program or the instructions given by the operators. Then, the control system sends out control signals to every actuator to control the coating process precisely. Meanwhile, the control system also has functions like fault diagnosis and alarm prompts to detect abnormal situations promptly and handle them properly for safe operation.
Summarize
The coating equipment will meet consumers’ needs better for high-quality, beautiful, and comfortable interiors of automobiles. This product will also greatly reduce the production cost and enhance production efficiency for automobile manufacturers