Huazhuo Plastic Welding Expert
Hot Plate Welding
Hot plate welding is the process of heating two pieces of plastic and pressing them together until they fuse. There are several different types of hot plate welding. Each technology differs in how they apply heat and pressure to the parts, but the basic steps are the same — add heat, apply pressure, and cool. Plastic welds are strong molecular bonds. Depending on which welding technology is used, the weld is hermetically sealed.
High efficiency and low cost:The Indispensable Role of the
hot plate welding machine in Automobile central controls
The HUAZHUO machine portfolio for hot plate welding is comprised of various sized standard machines for welding parts of different sizes. Common applications in the automotive industry include glove boxes,center consoles and map box linings. During hot plate welding, the plastic parts are welded using radiant heat and contact with an electric hot plate. Despite involving contact, this is a particle-free process that allows very strong and completely tight welds to be created for a number of different plastics.
Even thin-walled parts with complex 3D contours can be processed reliably with this well-established, robust process. Modern tool change systems, sophisticated drive technology, and the appropriate degree of automation increase productivity and make this fully developed process attractive for a number of industries and applications.
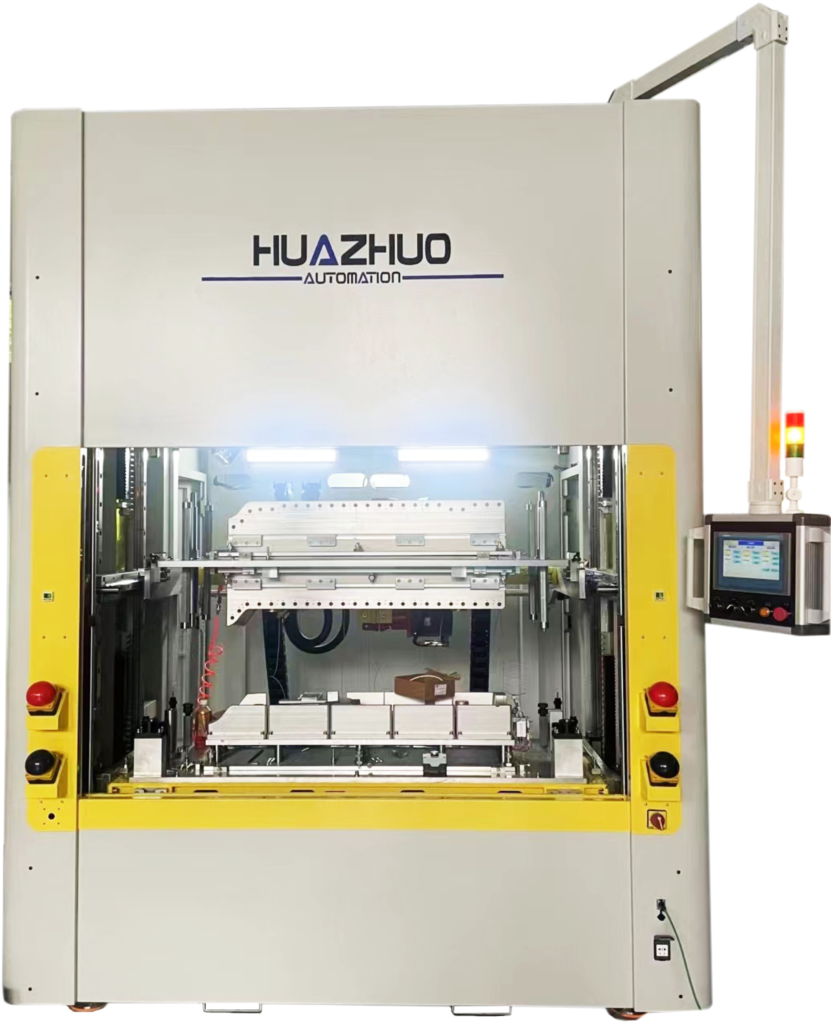
Modern contact welding
Hot Plate Welding Process
Hot plate welding is a multi-step process, as the heating and joining of the parts occur separately. After the parts are inserted into the fixture, they are placed against an electrically-heated plate. This contact with the hot plate begins the welding process, which is divided into three phases:
Melt, Open, Seal.
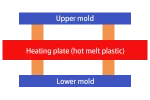
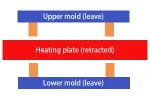
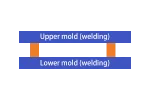
Large dimensions and complex geometries
HOT PLATE WELDING APPLICATIONS
- Large parts in the automotive industry, including instrument and door panels, center consoles
- Air or other filter housings
- Tank systems/tank filters
- Parts with complex 3D weld contours
- Air ducts
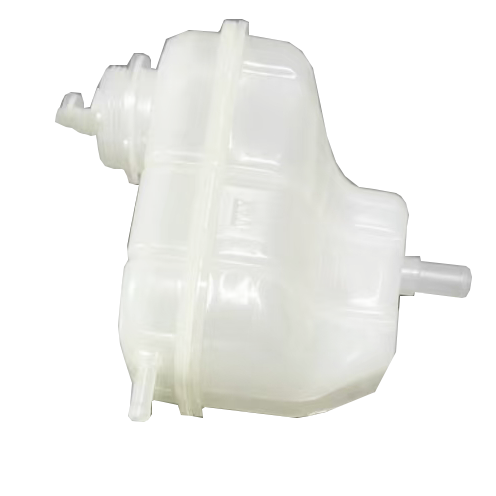
Hot plate welding cooling kettle
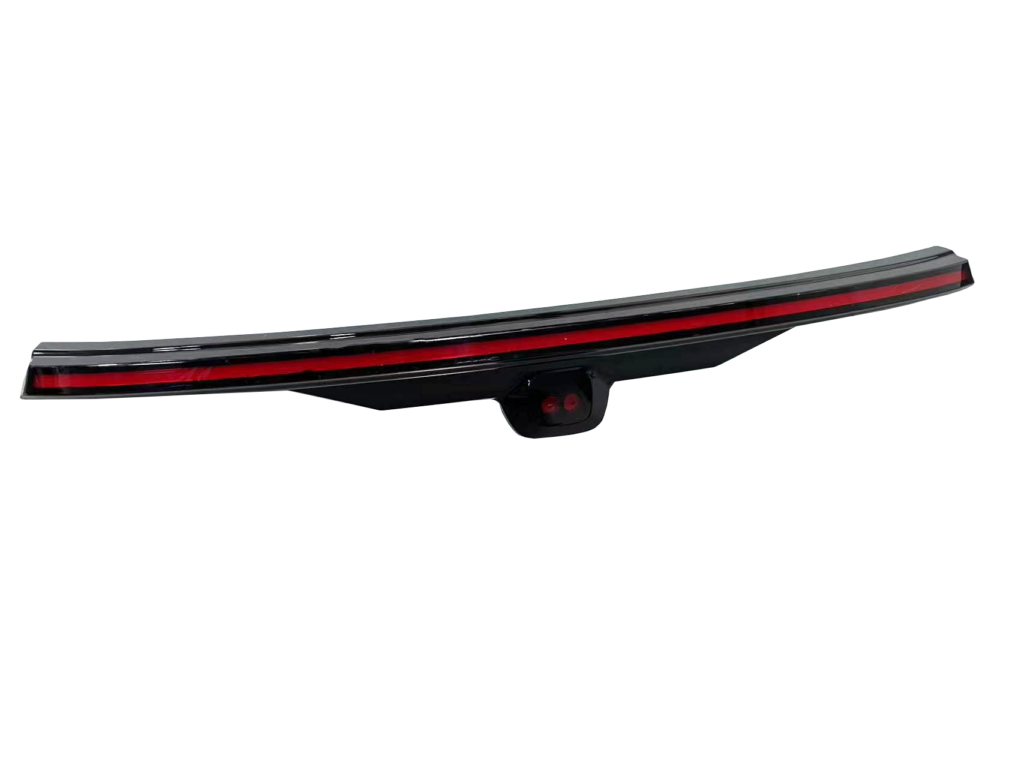
Hot plate welding car lights
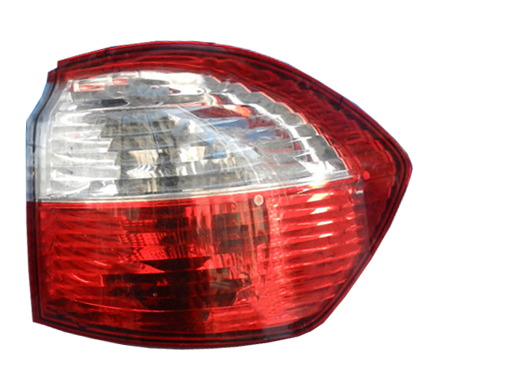
Hot plate welding car lights
HUAZHUO HOT PLATE WELDING MACHINE ADVANTAGES
Welding of parts with complex 3D weld contours possible
Strong, completely tight welds
Suitable for a wide range of plastics
Welding of large areas
Short cycle times for large lots
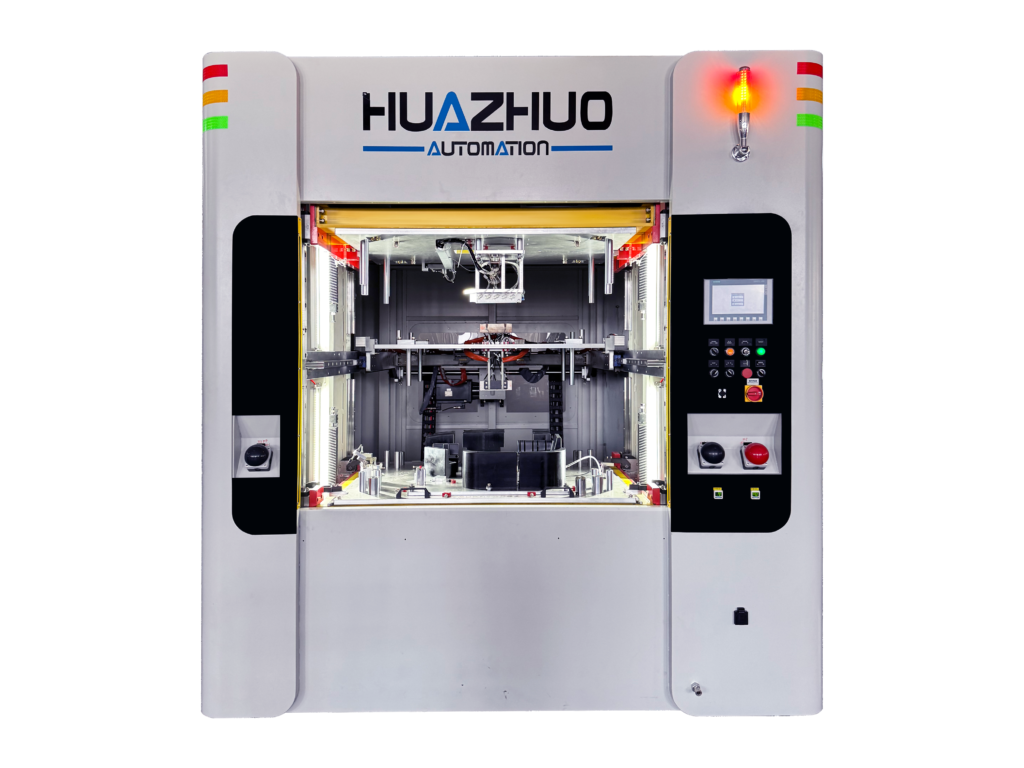
Equipment parameters
- Conveying motor: servo motor
- Power source: electricity + air pressure
- Cylinder: AirTac
- Hydraulic station: /
- Limiter control: cylinder
- Throttle adjustment: pressure regulating valve/proportional valve
- Machine dimensions: 2700*1900*1990
- Equipment weight/mold weight: 4T/1.5T
- Upper and lower mold dimensions: 855*500*450 (customized)
- Hot mold dimension: customized
- Equipment mold change position: front mold change
- Mold dimension: 1100*800*450
- PLC controller: Siemens
- Temperature control points: 8
- Upper and lower mold speed: customized
- Hot mold speed: customized
- PLC controller: Sienmens
- Mold closing pressure: according to product size
- Upper/lower mold weight: according to product size
- Hot mold mold weight: according to product size
- Equipment mold opening size: 1400mm
- Upper mold stroke: 300mm
- Position accuracy: 0.05mm
- Mold position accuracy: 0.1mm